BLOWING AND INJECTION PROCESSES
The process requires a machine called a blower. The material balls (PEHD, PA, etc.) are melted with an endless screw and fill an accumulation head.
Once the head is filled, a figure sinks and two half-shells are placed on it. With the mould closed, blowing fingers blow air to press the material onto the mould. The mould opens, a reservoir in the shape of the mould is produced. We then cut, weld and integrate the different components of a tank (valve, pump, sensors, pipes, etc.) on automatic and assembly lines.
We then check the tightness of each tank individually.
We use many different materials for all types of applications and test in our laboratory any new material that could bring a competitive advantage :
- Blowing: HDPE, AP…
- Injection: POM, PA, PBT, PP, PE, PC, ABS, PEI, SAN…
This process uses a machine called an injector press. The balls of material are melted and then injected under pressure into the hollow cavities of the moulds. The result is solid parts in the shape of the mould.
Through our parent companies, the RMT group has a quiz of injection moulding machines ranging from 25 to 260 tonnes.
We inject ourselves the automotive components needed for fuel circuits such as ventilation valves, caps, filling heads, pipettes…
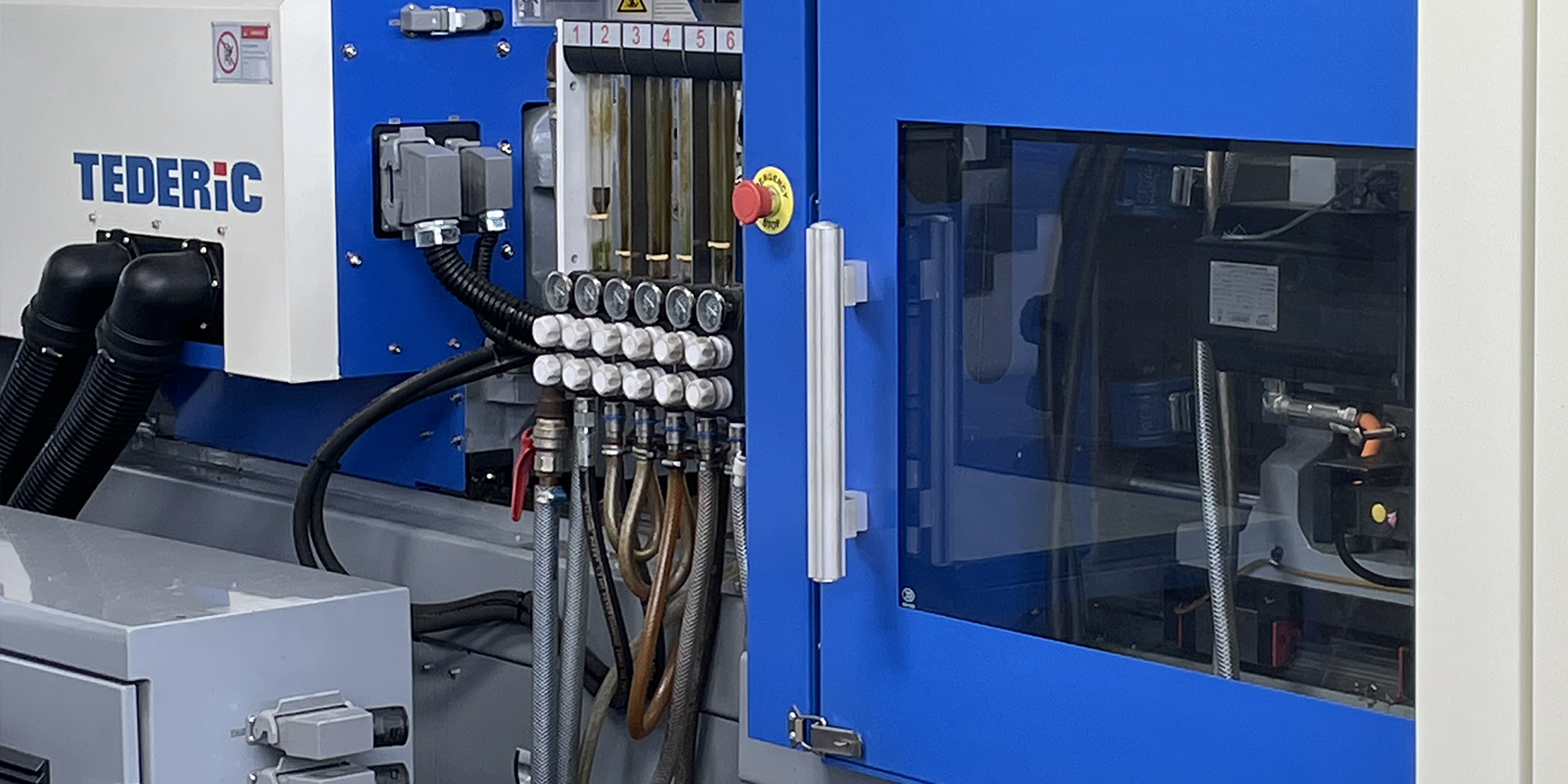